The Crucial Role of Quality Management Systems & ISO 13485 for medical device manufacturers – Part 3
- Louise Hollywood
- Oct 31, 2023
- 3 min read
Importance of Internal Audits and Management Reviews
Internal audits and management reviews are integral components of a QMS. They play crucial roles in ensuring the effectiveness of the QMS and the overall success of the organisation. Here's a closer look at the importance of internal audits and management reviews:
Internal Audits:
Identifying Non-Conformities: Internal audits involve a systematic examination of processes, procedures, and records. They help identify non-conformities, deviations, or areas where the QMS may not be functioning as intended. Detecting and addressing these issues early on can prevent regulatory violations, product defects, and quality problems.
Continuous Improvement: Internal audits are not just about finding problems; they are also an opportunity for improvement. They provide a mechanism for assessing the efficiency and effectiveness of processes and procedures. Organisations can use audit findings to identify areas for optimisation and enhancement, leading to increased operational efficiency and product quality.
Ensuring Regulatory Compliance: Internal audits provide a mechanism to assess the organisation's compliance with ISO 13485 as well as other applicable regulatory standards and requirements. This helps identify gaps and non-conformities, allowing for corrective actions to be taken promptly to maintain compliance.
Risk Management: ISO 13485 emphasises the importance of risk management in medical device manufacturing. Internal audits can assess the effectiveness of risk management processes within the organisation. This includes evaluating how well risks are identified, assessed, mitigated, and monitored. Effective risk management contributes to the safety and performance of medical devices.
Management Reviews:
Management Review: Management reviews are formal assessments conducted by senior leadership to evaluate the QMS's performance. These reviews ensure that top management is actively engaged in overseeing quality-related activities. Management reviews provide a platform for strategic decision-making, resource allocation, and setting quality objectives.
Monitoring Progress: Management reviews allow senior leadership to monitor progress toward achieving quality objectives and compliance goals. By reviewing key performance indicators and quality metrics, management can make informed decisions on how to address any identified issues or improvements needed to meet organisational goals.
Corrective and Preventive Actions (CAPA): management reviews play a critical role in the CAPA process. Reviews include discussion of non-conformities and assess the effectiveness of these actions and whether preventive measures are necessary to avoid recurrence.
Demonstrating Commitment to Quality: Regular management reviews demonstrate an organisation's commitment to maintaining a robust QMS and ensuring the quality and safety of its medical devices. This commitment is essential for building trust with regulatory authorities, customers, and stakeholders.
Internal audits and management reviews are not just routine tasks; they are essential processes within ISO 13485 that help medical device manufacturers maintain regulatory compliance, identify opportunities for improvement, manage risks, and demonstrate their commitment to quality. By systematically evaluating and reviewing the QMS, organisations can ensure the safety and efficacy of their products while remaining competitive in the highly regulated medical device industry.
Tips for Manufacturers
To ensure a smooth QMS operation and compliance with ISO 13485, manufacturers should consider the following tips:
CAPA Implementation: Don't hesitate to open CAPAs during internal audits. This demonstrates that your quality system is proactive and responsive to non-compliance issues.
Change Control: Manage all changes through a formal change control process to maintain document and process integrity.
Job Descriptions and Training: Ensure all job descriptions are signed and that employee training records are up to date.
Document Linkage: Ensure that all documents, including Standard Operating Procedures (SOPs), work instructions, and forms, are linked with each other to maintain consistency and traceability.
Quality Policy Awareness: Make sure all employees are trained and aware of the Quality Policy and Quality Manual to foster a culture of quality throughout the organisation.
Conclusion
A Quality Management System is indispensable for medical device manufacturers because it ensures regulatory compliance, product safety, consistency, and traceability. It promotes risk management, customer satisfaction, and continuous improvement while providing a competitive edge in a global market. ISO 13485 certification aligns manufacturers with international standards, making it easier to comply with regulations like the EU MDR. Timely implementation, internal audits, and adherence to best practices are essential for maintaining a robust QMS that ensures product safety and quality, safeguarding both patients and a manufacturer's reputation in the long run. Ultimately, a well-functioning QMS contributes to the overall success and sustainability of a medical device manufacturing company.
If you are a medical device manufacturer selling into the EU and have not yet transitioned to an EU MDR-compliant QMS or have not achieved MDR compliance for your products, it is essential to take immediate action to meet the regulatory requirements and avoid potential legal and market access issues. Additionally, manufacturers should stay informed about any updates or changes to regulatory deadlines and requirements, as regulatory authorities may provide further guidance or extensions in specific circumstances.
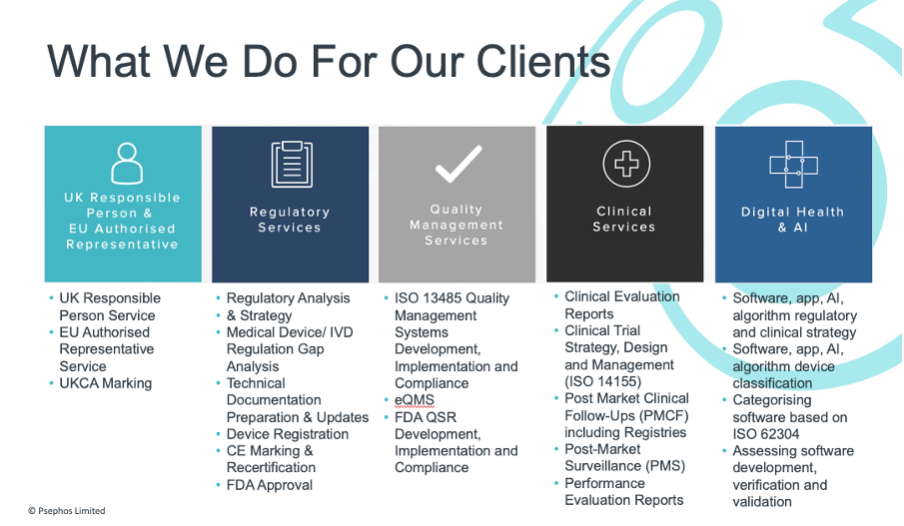